
Producing Macadamia Filament
The initial lab testing stage was completed at Chulalongkorn University in Bangkok, Thailand.
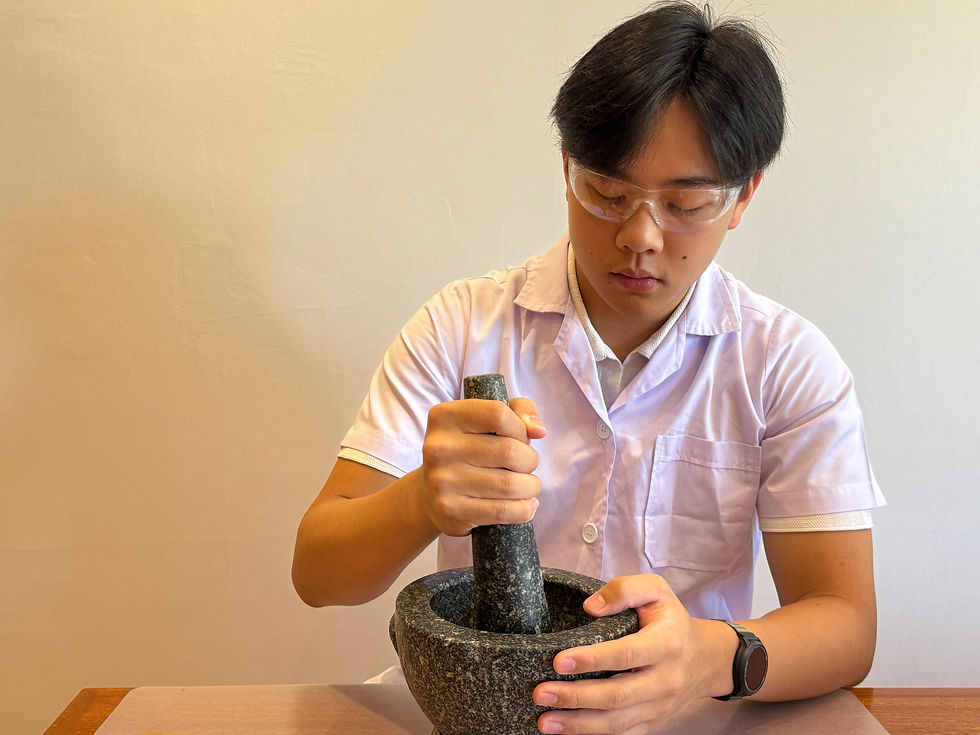


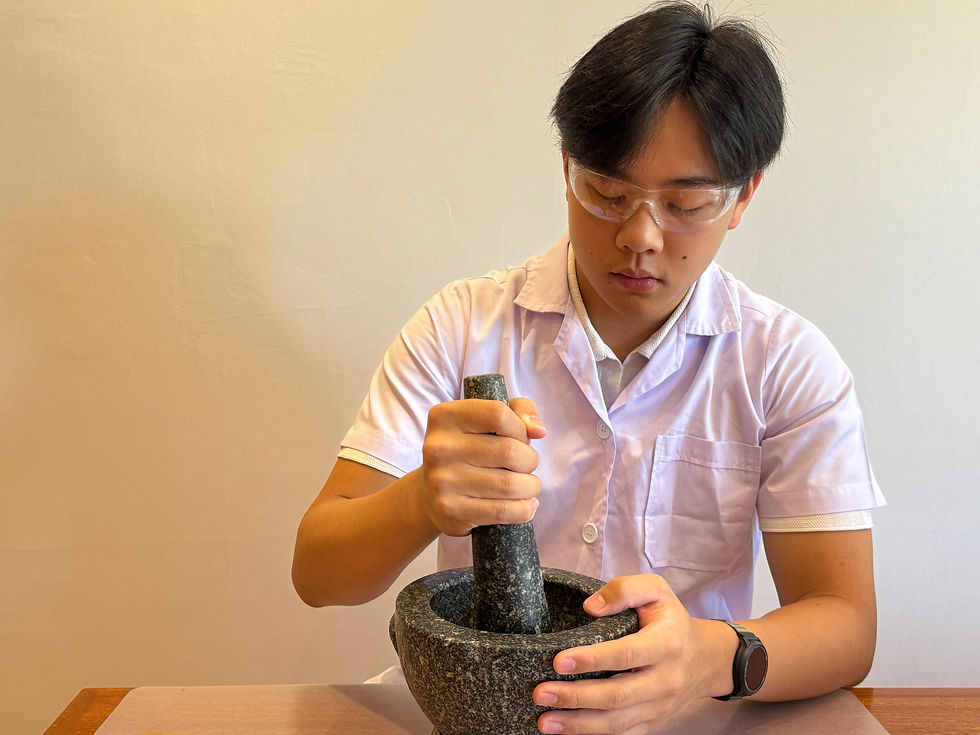
01
Reducing Macadamia Shell Size
To reduce the size of the macadamia shells, they are crushed in a mortar and blended. The smaller shell particles are dried at 60˚C for 4 hours and then sieved at 180 µm. Shell particles, < 180 µm, were collected and stored in a zip-lock bag.
02
Preparing Materials
Ingeo™ Biopolymer 4043D — Polylactic Acid (PLA) pellets, Macadamia Shell Powder (MC), Polypropylene Glycol 2000 (PPG 2000), and Maleic Anhydride (MA) are used in this experiment. PLA pellets are dried at 60˚C for 4 hours. 4 formulas were created and mixed.
1. PLA (300g)
2. PLA (282g) + PPG 2000 (15g) + MA (3g)
3. PLA (270g) + MC (15g) + PPG 2000 (15g)
4. PLA (267g) + MC (15g) + PPG 2000 (15g) + MA (3g)
03
Extruding
These 4 formulas are poured into a hopper of a twin-screw extruder from LabTech Engineering. After extruding, the filament passes through a water bath to cool down and is rolled into a spool. Each filament is then dried in an oven at 60˚C for 4 hours.
04
Printing
A tensile test sample (ASTM D638 Type 5) was printed 5 times each filament on a Raise3D Pro2 3D printer at 190˚C for the nozzle and 50˚C for the bed plate. Additionally, keychains are also printed in collaboration with Doi Tung Developmental Project.
05
Testing
Small pieces of each filament were cut out and separated. Each piece is dipped in liquid nitrogen, broken in half, and placed in a petri dish. The petri dishes are then dried in an oven at 60˚C for 4 hours. Each sample is carefully stuck to a metal block using carbon tape and labeled 7 to 10. Before Scanning Electron Microscope (SEM), the cross-section of each sample on the metal block has to be coated in gold. Each sample is zoomed 50x, 500x, and 1000x. The tensile prints are sent for testing, but is awaiting results.